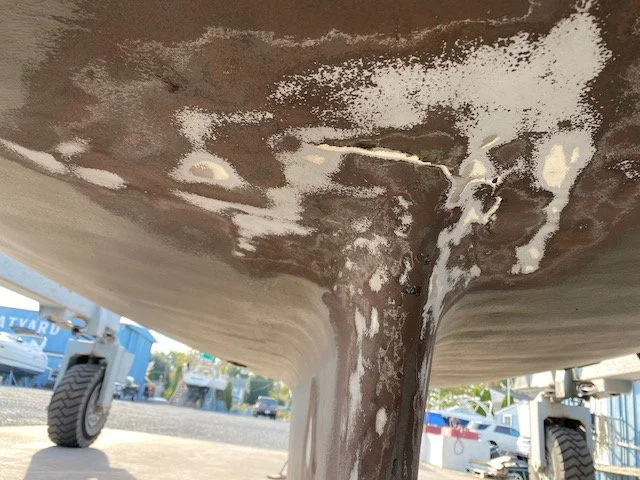
The surveyor just said he’s found some “wet spots”. What now???
On boats, moisture is the result of material degradation. As boats are exposed to all of the elements, degradation over time is inevitable. It's standard to find some moisture in older boat hulls due to factors like bedding failure, compound cracks, crazing, and compromised heavy load areas. The question is, where is the moisture and how extensive is it?
First, it’s important to understand how boat hulls and decking are made. There are two types of cored hulls.
-Balsa-Cored Hulls: Common in older boats, susceptible to moisture ingress, which varies based on location and size.
-Foam-Cored Hulls: A more modern technology with improved resin infusion techniques reducing moisture-related issues.
For this article we’ll focus on the older hulls. Balsa-cored hulls have been a significant part of boat manufacturing since their introduction in the 1960s. Despite the emergence of alternative core materials, many manufacturers continue to utilize balsa due to its favorable properties, such as strength-to-weight ratio and stiffness, which are highly valued in boat construction.
However, it’s important to note that the effectiveness and longevity of balsa cores are heavily dependent on proper installation and maintenance. When correctly implemented, balsa-cored hulls can offer durability and performance comparable to other core materials.
So if moisture or wet spots are discovered at survey, don’t panic. The impact of moisture can be different depending on where it’s found. We can classify a boat as having two basic areas:
No/Low Load Areas: Examples of no/low load areas would be the cabin interiors, flybridge, interior boat partitions, and the foredeck (on a powerboat). Many of the newer powerboats have a sun pad or other upholstery on the foredeck. These are notorious for getting wet underneath, especially if the owner never removes them. Moisture in these areas is less concerning, and discussion should focus on identifying and repairing moisture sources or just committing to keeping an eye on them.
High Load Areas: Moisture poses significant safety risks, such as compromised structural integrity leading to potential failures. Examples of high load areas are the hull bottom, the transom in a powerboat, and keel and centerline structures. Or at the base of the mast on a sailboat or any of the rigging chainplates, deck and hull junctions. High moisture readings in these areas mean further investigation may be necessary (such as taking a core sample to get more accurate readings). If you’re a buyer, high readings in these areas may be cause for considering other boats instead.
Rudders. These deserve their own paragraph. On powerboats, these are usually some kind of metal or carbon fiber. But on recreational sailboats, they’re almost always built like surfboards with fiberglass layers, metal supports, and foam cores. Expansion and contraction due to temperature changes tend to enable moisture ingress over time.
Signs of Moisture Issues in rudders are:
-Visual Indicators: Rust blisters, cracks, and bulbous formations on rudders.
-Survey Findings: Moisture meters and sound tests identify compromised areas.
Repair and Replacement: Delaminated rudders can be repaired or replaced, but assessing the extent of degradation is crucial for safety.
So, at the end of the day, if you are buying or selling a boat, how do we make sure that moisture is properly addressed?
For Boat Buyers:
Conduct Thorough Surveys: Use moisture meters and auditory assessments to evaluate hull integrity.
Evaluate Core Material: Understand whether the hull is balsa or foam-cored and the associated risks.
Assess Maintenance History: Check for regular re-bedding and repairs in documented inspections.
Budget Appropriately: Allocate funds not just for purchase but also for potential refits and maintenance.
Work with your broker to manage expectations. The older the boat, the more likely there will be moisture issues.
For Boat Sellers:
Schedule Regular Surveys: Perform moisture and delamination checks every 5-7 years as recommended.
Re-bed Through-Deck Fittings: Ensure all fittings are re-bedded periodically to prevent moisture ingress.
Monitor High Load Areas: Pay special attention to areas like transoms, engine mounts, and rudders for signs of moisture and delamination.
Work with your broker to assess any issues and either repair them before listing the boat or disclose them in the listing